Thermal Spray Wires
Babbitting with Thermal Spray Wires with Oerlikon Metco USA product. Babbitt, also called Babbitt metal or bearing metal, is any of several alloys used for the bearing surface in a plain bearing.

RE-BABBITT WHITE METAL SLEEVE BEARING http://www.stgwengineering.com
“Plain bearing” is a sliding bearing that receives a load through pressure. A plain bearing is often also referred to as “bushing”, “babbit” or “journal bearing”.

Crankshaft Bearing (image: http://rebabbittingbearing.com)
In general, plain bearings are cylinders which are halved and are called “shell” or bearing frames.
These bearings are very widely used and can be observed in various types of equipment, especially on crankshafts and crank rod bearings on vehicle engines.
Bearings can provide a low friction slip between two surface loads in contrast to other surfaces.
The movement of both can be in the form of a rotational axis (rotational movement) or linear motion.
Bearing frames are generally made of steel, cast iron, or copper alloys. The inner walls of these bearings are usually coated with a alloy of lead (Pb-base) or tin-white alloy (Sn-base) which is called a “babbit” metal.
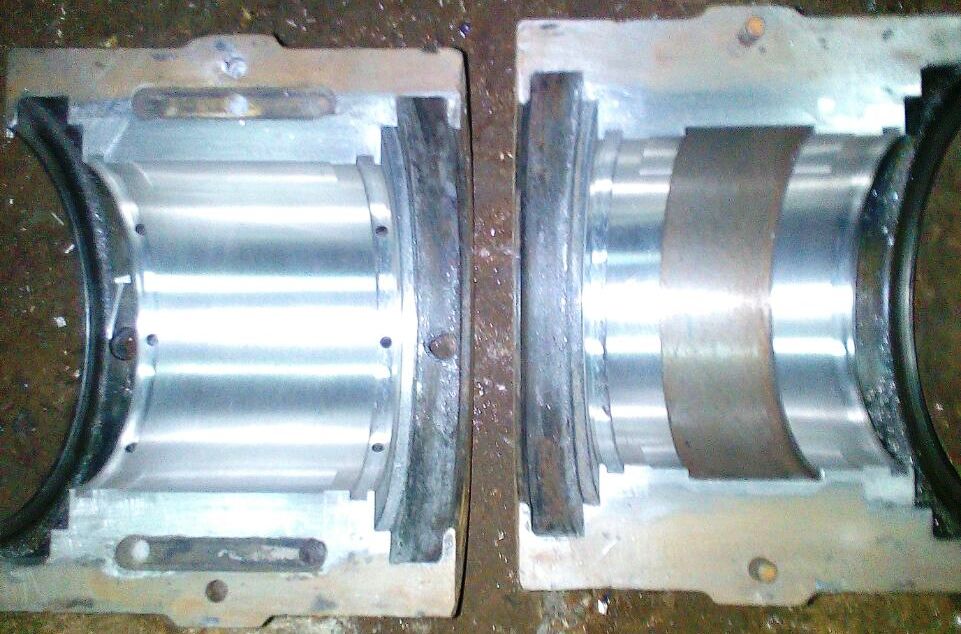
Crankshaft White Metal Babbitt Bearing pic: rebabbittingbearing.com
This babbit metal must be able to attach firmly to the bearing frame. As time goes by with a long service life, these pads will experience wear on the surface base metal which is influenced by various factors such as the load received is too excessive or the strength of the material itself.
In the field of maintenance, the bearing unit problem is one of the main problems, namely how to do it best repair on these bearings

Picture of bars and pigs of DuraKapp/Kapp Alloy #2 (Grade #2 Babbitt) – image credit: WillisPThomas
Referring to https://en.wikipedia.org/wiki/Babbitt_(alloy) explained that, the original Babbitt alloy was invented in 1839 by Isaac Babbitt[1] in Taunton, Massachusetts, United States. He disclosed one of his alloy recipes but kept others as trade secrets.[2] Other formulations were later developed.[3] Like other terms whose eponymous origin is long since deemphasized (such as diesel engine or eustachian tube), the term babbitt metal is frequently styled in lowercase.[3][4] It is preferred over the term “white metal”, because the latter term may refer to various bearing alloys, lead- or tin-based alloys, or zinc die-casting metal.
Microstructure of babbitt

Microstructure of babbitt – This is microstructure of bearing alloy babbit, which consists of (10 —12) % Sb; (5,5 —6,5) % Cu, remains Sn. (Pic: Edward Pleshakov)
Babbitt metal is most commonly used as a thin surface layer in a complex, multi-metal structure, but its original use was as a cast-in-place bulk bearing material. Babbitt metal is characterized by its resistance to galling. Babbitt metal is soft and easily damaged, which suggests that it might be unsuitable for a bearing surface. However, its structure is made up of small hard crystals dispersed in a softer metal, which makes it a metal matrix composite. As the bearing wears, the softer metal erodes somewhat, which creates paths for lubricant between the hard high spots that provide the actual bearing surface. When tin is used as the softer metal, friction causes the tin to melt and function as a lubricant, which protects the bearing from wear when other lubricants are absent.
Internal combustion engines use Babbitt metal which is primarily tin-based because it can withstand cyclic loading. Lead-based Babbitt tends to work-harden and develop cracks but it is suitable for constant-turning tools such as sawblades.
The surface of the wearring that has undergone wear requires re-coating to restore the surface to its original condition.
Babbitt coating can use a variety of techniques: with casting techniques, welding techniques or spray techniques. Of the three techniques each has its own flaws and advantages.
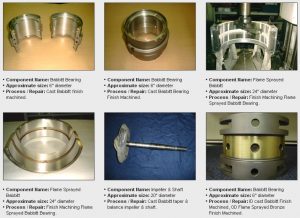
Sample Cast and Flame Spray Component Projects – http://www.bbcmachine.com/cast-flame-spray-repair-babbitt-bearings.html
The welding technique used is using GTAW (Tungsten Arc Welding Gas).
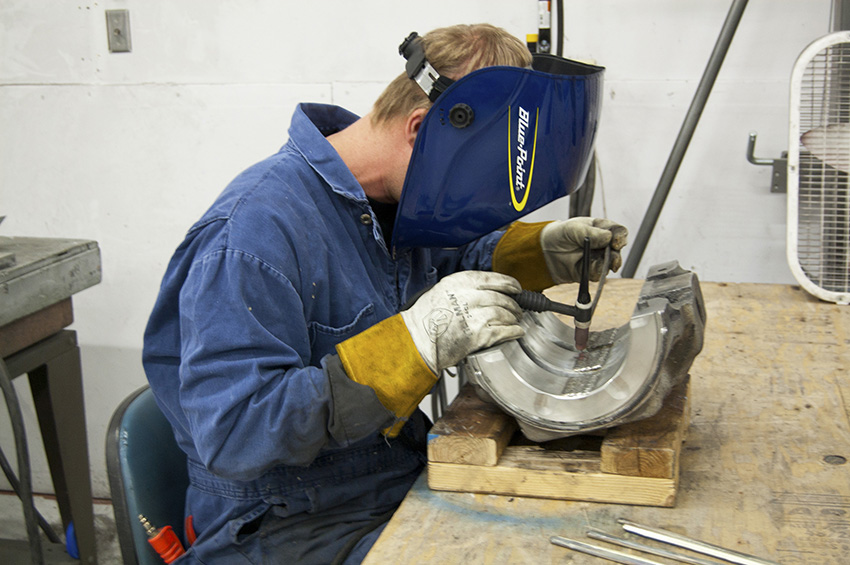
The babbitt coating technique using a welding technique http://www.dxpbabbitt.com/repair/
Our company accept orders for welding wire rebabbit with the brand Oerlikon.
The following are OERLIKON product technical specifications.
Thermal Spray Wire – OERLIKON METCO
Materials : METCO Flame Wire ( Bonding Metco 405 NS, Metcoloy 2, SpraBabbitt A, SpraSteel etc. ), Arc-Spray wire, Equipments : Wire Flame Gun type 14E, Powder Flame Gun type 5PII & 6PII

sprababbit A wire from oerlikon metco USA product
Sprababbitt A is a special high grade, tin-based babbitt wire that is manufactured exclusive for thermal spray. Coatings of Sprababbitt A are particularly suitable for high speed and heavy duty bearing surfaces that required coatings of the highest possible quality, especially for critical applications.
The coatings are ductile, low in oxides and exhibit a bright, metallic appearance.
Sprababbitt thermal spray wires are designed for application using electric arc wire spray or combustion wire spray.

sprababbit A wire from oerlikon metco USA product
Oerlikon Metco Material Product Data Sheet – Tin and TinAlloy (Babbit) Thermal Spray Wires
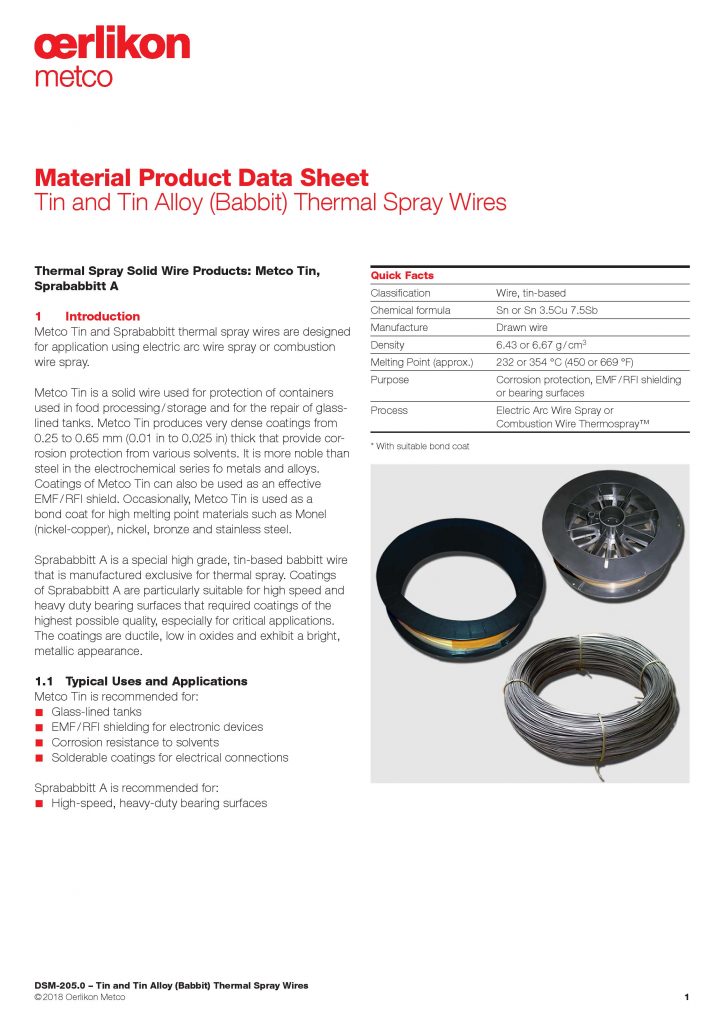
Data Sheet of tin and tin alloy (babbit) Thermal Spray Wires
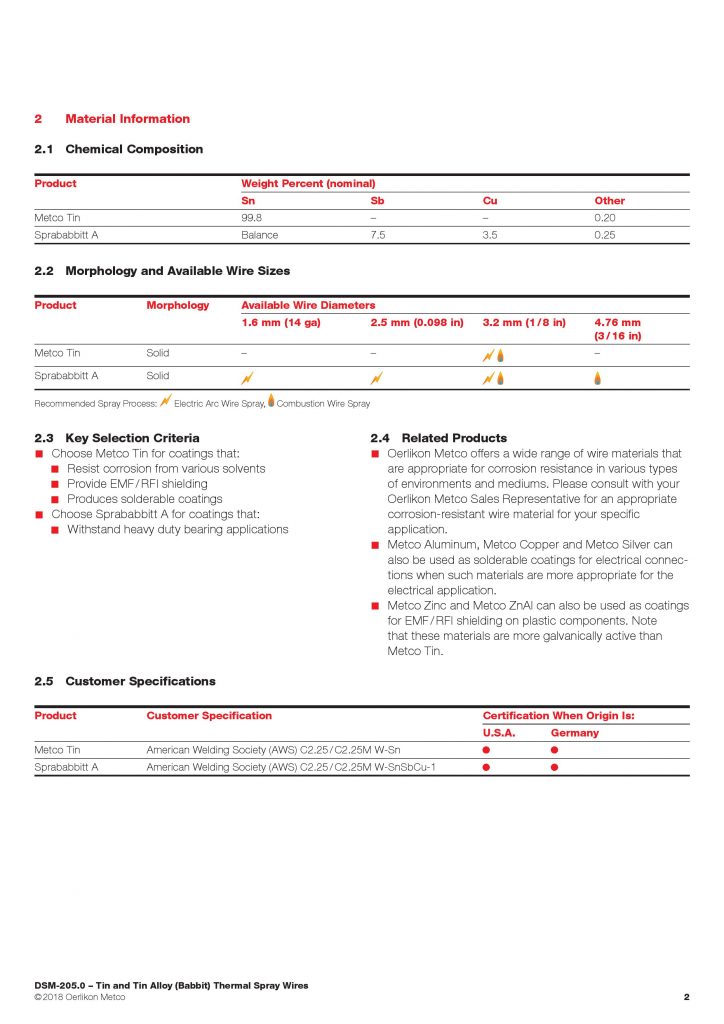
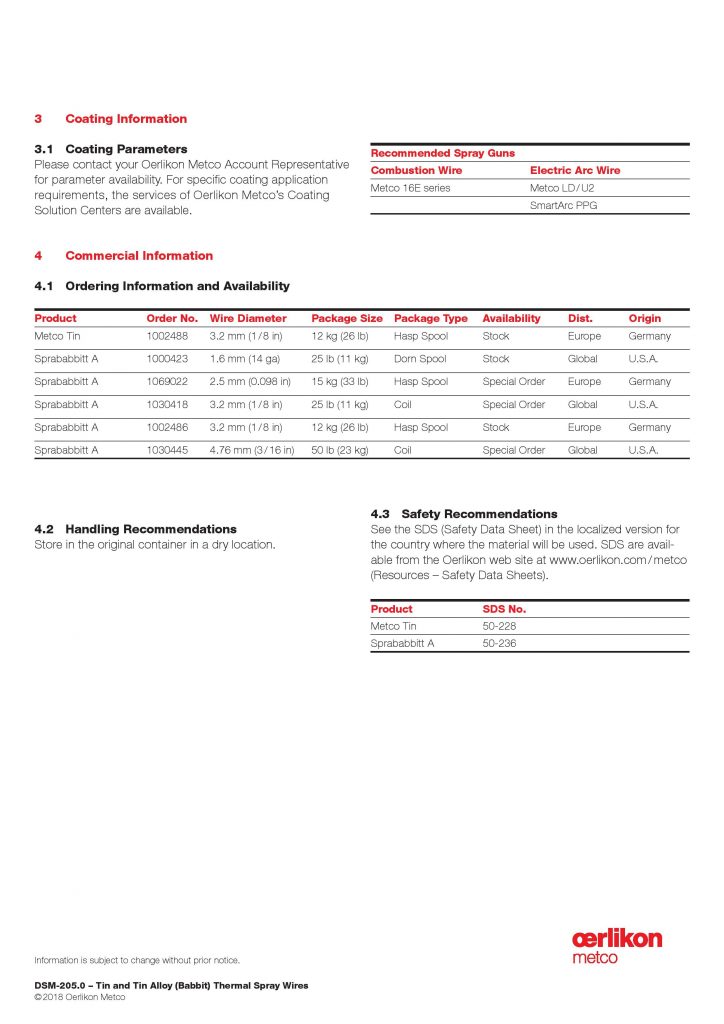
Babbitting withMetco 16NCS self fluxing nickel base alloy powder from Oerlikon Metco product

we would like to have the data sheet for part No.1000423 and 1030418, yr kind attention are very appreciated, thanks
Best Regards
Alpin Wu
Please give me inquery Spprababbit A Pn. 1030418
Thanks
Irwan
Mhn info kebutuhannya berapa rollkah?…bisa email ke [email protected]
Terima kasih